A cutting-edge relationship: how one sawmill business trimmed its energy costs
Cutting timber is a power-hungry business, but E.ON can help save precious pounds in energy expenditure
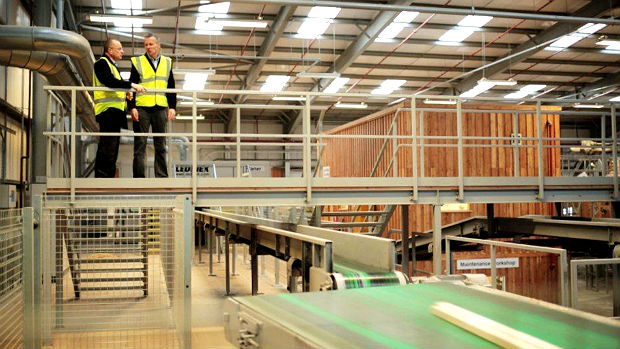
For many manufacturing businesses, energy costs represent a substantial slice of total annual expenditure – which means that getting the right deal will have a significant effect on a company's bottom line.
One such energy-intensive company is the BSW Timber Group. With eight separate sawmilling operations – seven in the UK and one in Latvia – BSW currently spends between £4m and £4.5m per year on energy.
Kevin Young, the company's group purchasing manager, was therefore more than willing to listen to E.ON's proposals when the company called to discuss BSW's energy needs.
The Week
Escape your echo chamber. Get the facts behind the news, plus analysis from multiple perspectives.
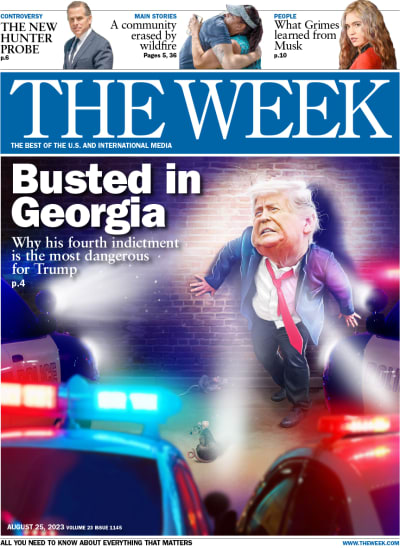
Sign up for The Week's Free Newsletters
From our morning news briefing to a weekly Good News Newsletter, get the best of The Week delivered directly to your inbox.
From our morning news briefing to a weekly Good News Newsletter, get the best of The Week delivered directly to your inbox.
"Our current contract was coming to a close, so it was an opportune time," Kevin says. "E.ON are a known entity, they're not a small broker. And E.ON Portfolio Solution – EPS – were known to us."
The result of the conversation was a relationship in which E.ON provided BSW with a great deal more information about how BSW was consuming – and paying for – energy. As Kevin points out, they have taken a very active approach.
"E.ON and EPS have given me a significant breakdown, not just transparency and visibility of what energy prices are doing going forward and how they will affect our business, but I can now see very specifically the effect of different third party charges on our costs," Kevin says.
"It's been very, very hands on. Our E.ON account manager has been to a number of our sites and presented what they can do for us."
Nor has the exchange of information been only in one direction.
"On top of that I went across to Düsseldorf and met our EPS portfolio manager and had a look at their systems," Kevin says. "Since then, there have been a number of initiatives implemented here in the UK looking at opportunities, efficiencies and how E.ON can help us.
Specifically, that meant the opportunity to save money both on peak electricity and Triad charges – the extra charges levied for three periods of peak demand between November and February, which the National Grid uses to set transmission fees.
"A big initiative they helped me with was focusing on peak energy periods and how we could potentially adjust shift patterns to miss those periods and save money," Kevin says.
The relationship between E.ON and BSW is still in its relative infancy, so pinning an actual pound figure to the cost saving is difficult at this stage.
"I can't put a saving on what we've actioned so far," Kevin says, "but we're now missing the peak periods and avoiding Triad charges at two of our sites. This gives a two-fold benefit to this activity, and E.ON have helped us greatly by highlighting the opportunity.
Kevin is quick to point out that energy is a "necessary evil" when it comes to manufacturers and other energy-intensive industries. Power is at the heart of what they do, but they can also take responsibility for getting the most out of what they consume.
"Without energy we can't run the sawmill," he says. "But it was actually trying to switch our employees' mindsets to realise there are things you can do to make a difference.
"What has fallen out of all of this is initiatives to reduce energy costs and make us more efficient with our energy. Where you make the saving is simply by using less."
For more information visit eonenergy.com/EPS
A free daily email with the biggest news stories of the day – and the best features from TheWeek.com