The evolution of manufacturing
The manufacturing industry is one of the oldest on the planet, but how has it changed?
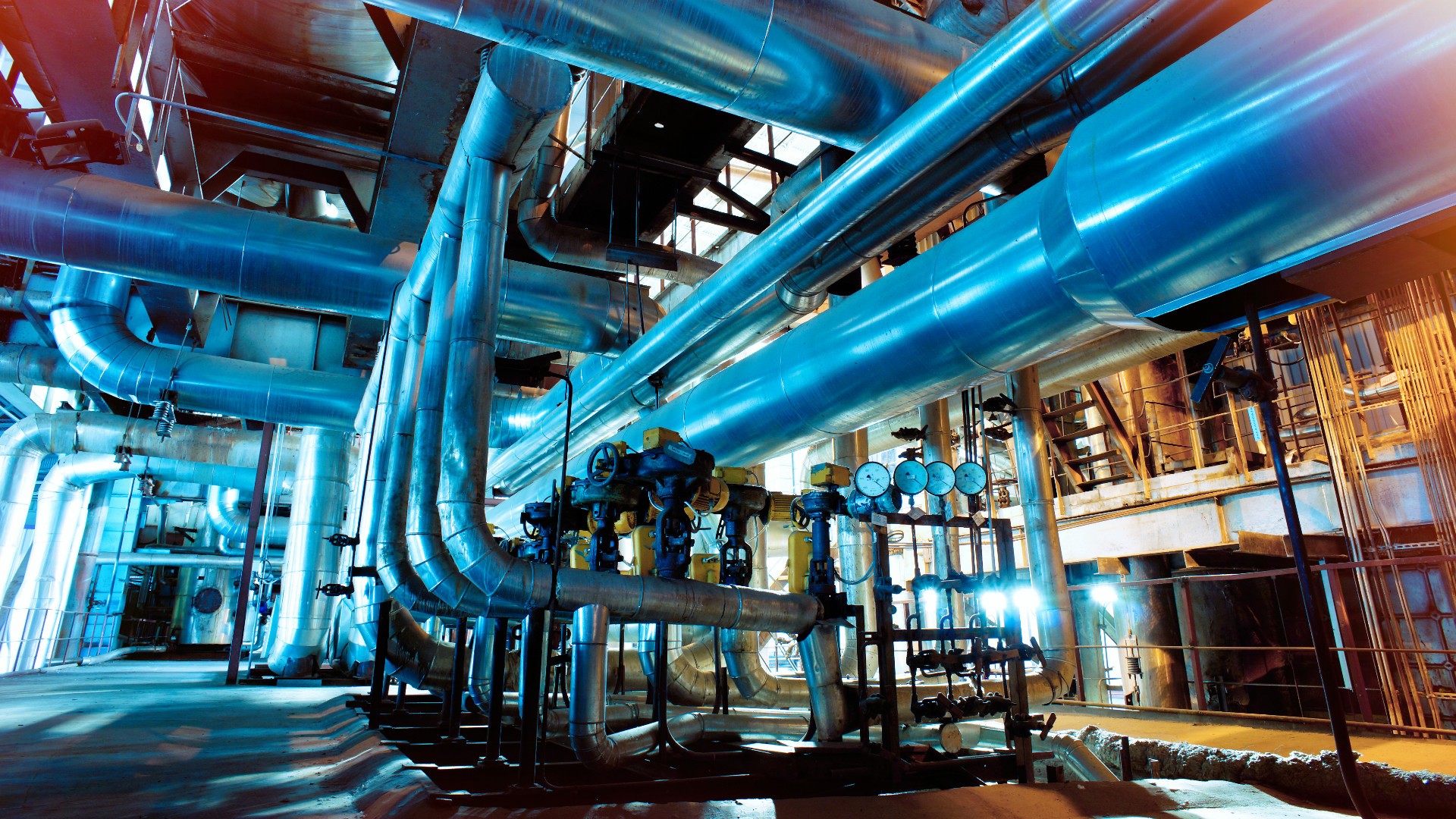
Manufacturing is undergoing a revolution. A revolution the World Economic Forum calls the industry’s greatest change in more than 100 years. First came the tools, then came the robots and now an industry that was once the backbone of the UK is turning to AI, the cloud and smart energy to reassert its dominance on a global scale.
The industry has undergone a tumultuous few decades. It’s been in relative decline since the 1970s, when it accounted for 27% of the UK’s economic value. By 2017, this figure was 10%. Yet, output is higher. We’re producing more now than we were almost 30 years ago – 6% more – but high production costs, cheaper imports and fast growing economies in the East have damaged our bottom line. The key to success is to make our industry more efficient and attractive; to use the latest advances in technology to bring back the innovation that saw Britain soar during the first Industrial Revolution two centuries ago.
By embracing technology, the manufacturing industry has the potential to completely transform itself – from efficiency on the factory floor, where tech such as AR and 3D printing could become commonplace, to distribution and delivery of the final product. But, to understand where manufacturing is going, it’s important to know where it began. In this feature we’ll explore manufacturing’s journey, and how we’ve gone from the machine-driven Industrial Revolution to Industry 4.0 and the cutting edge of technology.
Subscribe to The Week
Escape your echo chamber. Get the facts behind the news, plus analysis from multiple perspectives.
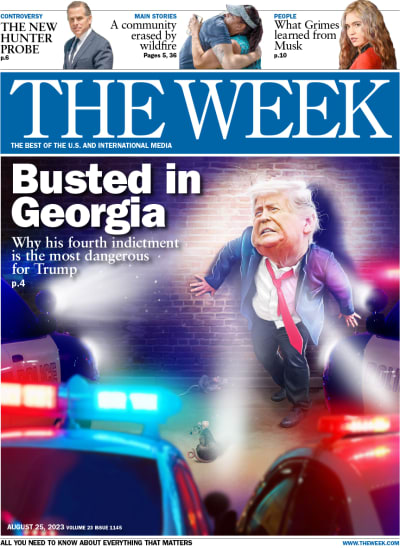
Sign up for The Week's Free Newsletters
From our morning news briefing to a weekly Good News Newsletter, get the best of The Week delivered directly to your inbox.
From our morning news briefing to a weekly Good News Newsletter, get the best of The Week delivered directly to your inbox.
In fact, Britain is classed as the birthplace of this original revolution. In the early 19th century, it was the world’s leading colonial power. The land not only had coal and iron ore deposits to help literally fuel the rise of industry, Britain could harvest raw materials from its colonies, especially India’s cotton, and export goods with ease. The demand for goods drove up innovation and this innovation was the catalyst for some of the most important manufacturing technological advancements of the past 200 years.
Britain expands its trade
As demand for goods grew, so too did Britain’s economy, putting pressure on existing infrastructure. Iron was used to revolutionise transport networks, including bridges and railroads, and the new steam train could transport vast amounts across the country, and beyond, with relative ease and speed. Along with the transport of goods, trains and roads meant people were more free to move, taking innovative ideas with them and spreading best practices. Thus, globalisation as we know it was born. Once Britain had set the groundwork for such an industrial transformation, the inventions, machines and work ethic was adopted more widely. In return, Britain “imported” the advancements in electricity from the US.
As the world prepared for the First World War, the second industrial revolution took hold. Demand for steel ramped up and electricity was used to create mass production. This fuelled further innovation, and the telephone, light bulb and internal combustion engine were all products of this time. During the decades that followed, businesses were able to expand internationally and mines and steelworks, as well as textile industries, provided huge employment opportunities.
It wasn’t until the 1980s when digital technology began to rise that the third industrial revolution laid down roots. And while it promised to revolutionise our lives, over the past 30 years it has seemingly damaged some of the working practices that came before. More than 600,000 jobs have been lost across the UK manufacturing sector over the past decade. Globally, this has been on a downward trajectory for the past five decades, dropping from around 25% down to around 12%.
It doesn’t mean it’s dead and buried though. Far from it. Towards the end of 2018, there was a small rise of 0.3% – a flicker of light. This is because “traditional” manufacturers are evolving to embrace digital transformation; they’re using artificial intelligence, remote management and the cloud to become increasingly efficient, dynamic and, most importantly, profitable.
Powering Industry 4.0
And, at the heart of this transformation, is energy. Coal powered the first revolution, electricity powered the second and third and a more efficient, sustainable use of energy will be needed in abundance for the fourth. A report from energy provider E.ON found that more than half of businesses believe their energy running costs are directly affecting how competitive they can be, with other industries within the UK and abroad. More than 91% said they’re keen to reduce their usage, as a result.
E.ON recently partnered with the AI experts at Sight Machine whose platform uses artificial intelligence, machine learning, and analytics to help customers track productivity. The partnership lets businesses avoid power cuts, prevent production bottlenecks, optimise energy usage and analyse data from multiple sites. All done by leveraging the power of the cloud.
In total, E.ON’s solutions claim to be able to save businesses up to £600,000 a year on energy and maintenance costs. This includes up to 20% using combined heat and power (CHP), which uses the heat generated when a business produces electricity for hot water and heaters. Productivity, and in turn, profit, can also be increased by generating energy on-site. British tiling experts Russell Roof Tiles saved £72,000 in a year thanks to CHP. Reckitt Benckiser is using CHP to cut its annual energy costs by a fifth, thanks to 24-hour remote monitoring. What’s more, a report from independent analyst firm Verdantix found that having greater control of energy on-site could save UK businesses – and the manufacturing industry – up to £33bn.
One of the biggest challenges to these changes, though, is the rise of services, and one of the largest definers of the fourth industrial revolution is a move away from mass production towards a more personal, customised experience. As manufacturing, has declined, the service industry has grown. At the end of 2018, the sector was the largest contributor to GDP growth across the UK. That doesn’t mean, however, that the two can’t work in harmony. In addition to the hardware provided by E.ON to manufacturing companies, it has effectively created “energy-as-a-service.” By enabling businesses to track their usage, business leaders can proactively manage what is being used, and E.ON helps them with this monitoring and gives tailored advice. Its energy consultancy tracks the energy market to make this advice as relevant as possible, while its data solutions team creates visualisations that let business leaders see where savings can be made, and how they can reduce emissions. The latter point is key. For energy efficiency solutions to succeed and have longevity, they need to benefit the environment as well as the customer. Britvic, using E.ON’s platform, recently moved to 100% renewable energy across its UK sites; saving up to 17,000 tonnes of CO2e a year – the equivalent to taking 3,300 cars off the road.
The future of manufacturing
These perceived threats can also be seen as opportunities. Manufacturing drives innovation – a report from the UK government found that manufacturing businesses are more likely to engage in research and development, and are more likely to innovate.
Take, for instance, the growth in 3D printing, which is poised to make huge waves in the manufacturing industry going forward. According to Deloitte’s recent report, Exponential technologies in manufacturing, the 3D printing market is expected to rocket from $13 billion (£9.87 billion) in 2016 to $36 billion ($27.32 billion) by 2021. It’s estimated that by 2020, 75% of worldwide manufacturing operations worldwide could use 3D-printed tools, jigs and fixtures in the production of finished goods. The Deloitte report states that potential future applications could revolutionise the automotive industry, with 3D materials used to make improved vehicle and aerospace parts. The increase in 3D manufacturing speed will enable faster production of 3D-printed products, bringing materials to sectors such as housing and construction and improving efficiency.
Meanwhile, tech like smart sensors are helping businesses become more efficient, and safer, and in the future, factories will rely ever more on the cloud. Applying data analytics, for example, could turn machinery maintenance from a reactive to proactive process. Anomalies collected via smart sensors and spotted by an analytics platform will be able to alert the factory floor when a machine is about to break instead of after the fact.
Automation will take over the tedious manufacturing jobs, leaving humans to be more creative, more innovative and more efficient. Data from augmented and virtual reality, and customer behaviours, will continue to help companies more efficiently invest in research and development, giving consumers more of what they want, getting it to them faster and cutting down on costs.
The emergence of augmented reality, while beneficial from a consumer standpoint, can also help shape the manufacturing workforce of tomorrow. Informational displays across dials and screens will move to field-of-view in an AR headset, while digital 3D renderings of working manufacturing equipment will mean technicians will be able to carry out jobs in a safer and more efficient way. Utilise it properly, and augmented reality has the potential to slash downtime, minimise errors and carry out daily tasks (for example, calling up inventory info or checking material delivery) without holding up production.
All of this will require manufacturers to adopt high standards when it comes to the transformation of the factory floor. New tech must meet safety regulations, while equipment lifespan, battery life and durability has to be taken into account. Plus, the speed and low latency of 5G will be needed to drive everything forward.
These may present the manufacturing industry with its greatest change (and challenges) in 100 years, but with the right attitude and a commitment to innovation, it could be the revolution that puts it back on top.
A free daily email with the biggest news stories of the day – and the best features from TheWeek.com
-
8 hotels with ace tennis courts
The Week Recommends Bring your A game
-
Abrego released from jail, faces Uganda deportation
Speed Read The wrongly deported Kilmar Abrego García is expected to be detained at an ICE check-in and deported to Uganda
-
Kyiv marks independence as Russia downplays peace
Speed Read President Vladimir Putin has no plans to meet with Zelenskyy for peace talks pushed by President Donald Trump