How trees inspired the renewable plastic of the future
This tough new material could revolutionize manufacturing
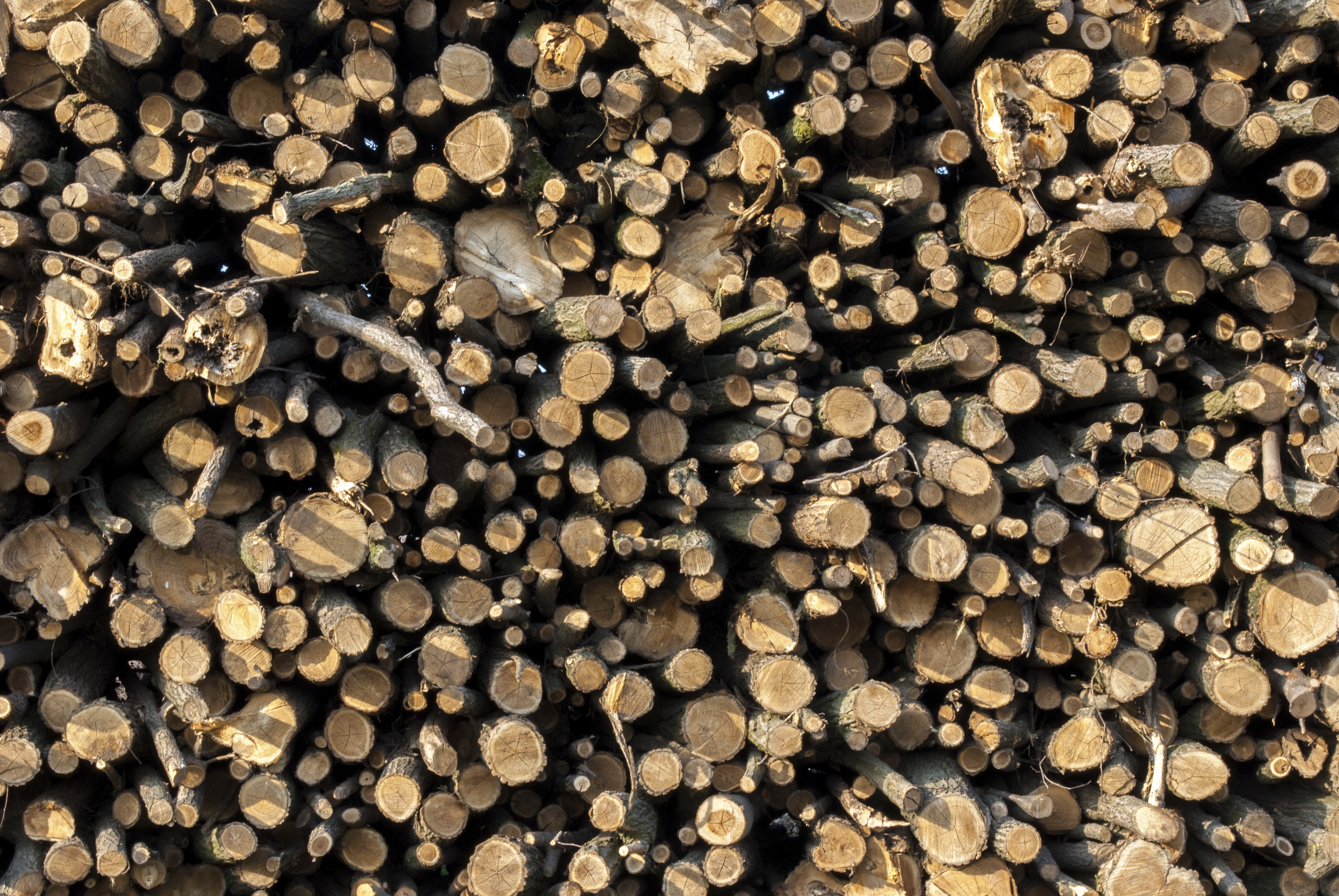
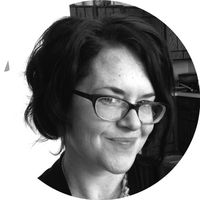
What's Earth's second most abundant organic material after cellulose? If the question leaves you scratching your head, look up at a tree while you do. Inside, you'll find lignin, the glue-like stuff that fills gaps in trees' cell walls and makes wood hard. It's the secret sauce in a newly developed polymer that could change how people think about plastic.
Researchers from Oak Ridge National Laboratory in Oak Ridge, Tennessee, recently announced that they've invented a tough, renewable polymer with the help of the substance, which fittingly has been called "nature's plastic." Its inventors think that one day it will replace polymers like ABS, which is used in everything from Lego blocks to motorcycle helmets.
If that's true, the change will be a welcome one: ABS, which stands for acrylonitrile, butadiene, and styrene, isn't recyclable or particularly sustainable; its production relies on natural gas or petroleum, neither of which are renewable resources. In the past, manufacturers have struggled to find a way to replicate ABS' strength and rigidity. For example, LEGO plans to phase out ABS by 2030, but has struggled to create an environmentally friendly replacement for the plastic.
Subscribe to The Week
Escape your echo chamber. Get the facts behind the news, plus analysis from multiple perspectives.
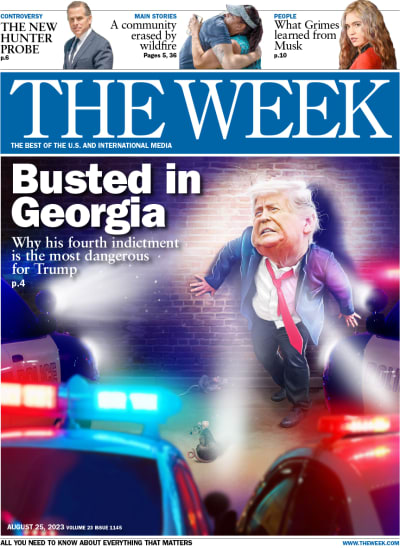
Sign up for The Week's Free Newsletters
From our morning news briefing to a weekly Good News Newsletter, get the best of The Week delivered directly to your inbox.
From our morning news briefing to a weekly Good News Newsletter, get the best of The Week delivered directly to your inbox.
That's where the Oak Ridge laboratory comes in. Amit Naskar, a materials scientist who leads the lab's carbon and composites group, honed in on a simple solution to the ABS problem. Why not replace the S in the equation — styrene, a nasty petroleum-based substance that's also a fuming volatile organic compound — with something renewable instead?
Taking a cue from trees, the team quickly turned to lignins. Currently, pulp mills extract lignins from wood as part of the manufacturing process; since they hold a tree's cellulose, or fiber, together, lignins have got to go to break the wood down. The byproduct is primarily used to make wood pellets that heat houses or is simply burned in industrial boilers. "We can do better than that," Naskar recalls thinking. He wondered if nature's plastic might live up to its promise.
The team members began to experiment with lignin. After evaluating different types — lignins vary in stiffness from species to species — they decided that lignin from hardwoods like oak are the most stable. Then they got to work coupling hardwood lignin with soft rubber containing acrylonitrile and butadiene. The result was softer than lignin, but harder than rubber, so they tweaked the amounts of all three substances and fiddled with heat levels to find the perfect conditions to generate an ABS-like polymer.
They succeeded. The new polymer is called ABL, and it has lots of perks. It's free of fuming solvents like acetone and chloroform, recyclable, and 50 percent renewable. ABL is tough, too: It can withstand 10 times the stress of its counterpart.
A free daily email with the biggest news stories of the day – and the best features from TheWeek.com
The team isn't done yet, though. "There are certain challenges associated with this material," says Naskar. It isn't yet clear whether ABL could be injected like ABS into molds to create custom shapes — a method used frequently in the automotive industry — and the team is still trying to find the best way to work with it. So when might ABL come on the commercial market? "I cannot predict that," says Naskar. "It would depend on whoever wants to use this kind of material."
Still, even with plenty to do before ABL is ready for prime time, the prospect of turning a solvent-heavy, non-recyclable plastic that's widely used into one that's renewable, recyclable, and less prone to off-gassing fumes is intoxicating to researchers. In a paper announcing the new plastic, the team wrote that commercialization could offer an additional revenue stream to biorefineries and pulping mills. That's not to mention the public relations boost it could give companies like LEGO, which could add a bit of polish to their sustainable halo if they switched to renewable plastics. When it comes to creating industrial plastics, perhaps the best way to preserve nature is to imitate it.
Erin Blakemore is a journalist from Boulder, Colorado. Her work has appeared in The Washington Post, Time, Smithsonian.com, mental_floss, Popular Science and more.
-
What is Linda Yaccarino's legacy? And what's next for X?
Today's Big Question An 'uncertain future' in the age of TikTok
-
The Pam Bondi and Dan Bongino schism threatens Trump's DOJ
In the Spotlight Two MAGA partisans find themselves on either end of a growing scandal over Jeffrey Epstein and his ties to White House officials
-
8 ways Trump's bill will change your taxes
The Explainer The 'big beautiful bill' was recently signed into law. Here's what it might mean for your wallet.