Automation and the productivity challenge: how Swiss Laundry embraced change
Lombard is helping a linen hire and laundry firm adopt new technology and increase productivity
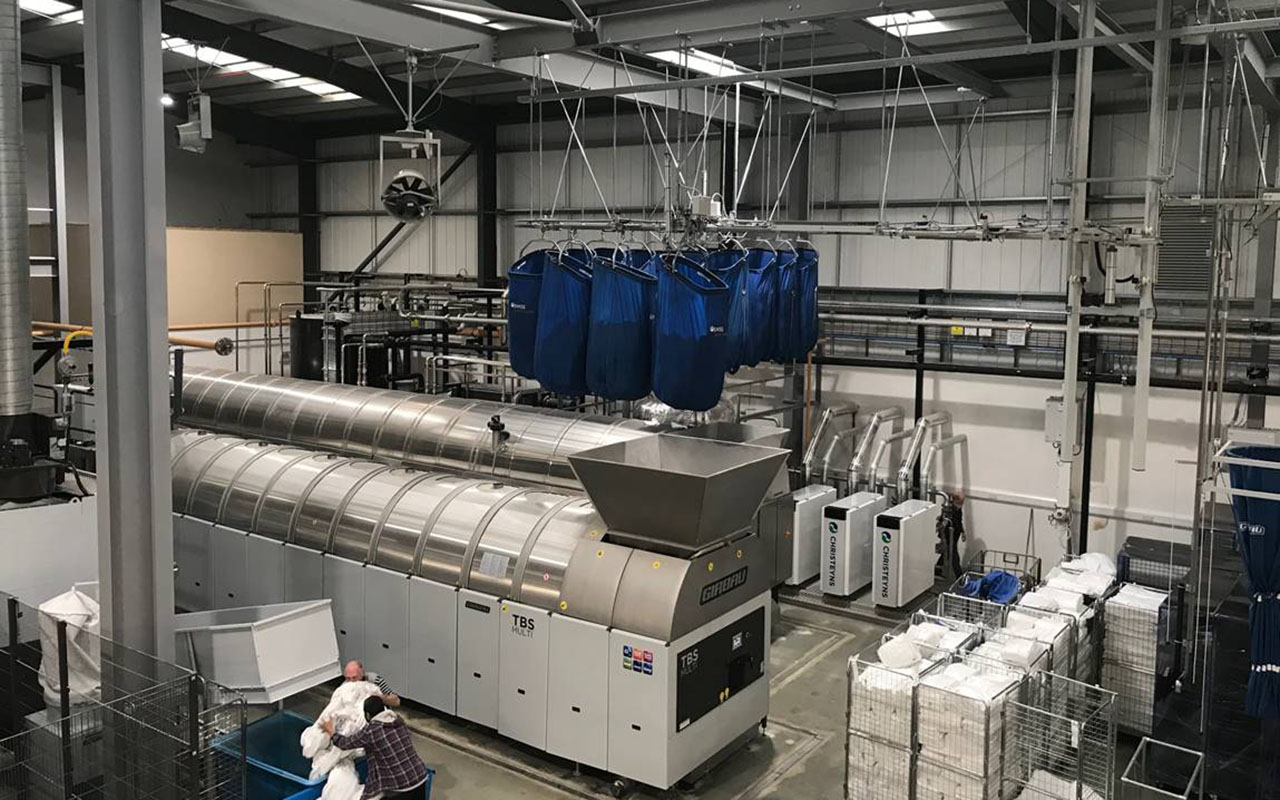
Guy Turvill is the third generation of his family to run Swiss Laundry, one of the largest independent hospitality linen hire and laundry suppliers in the UK. Now chairman, he has spent almost a quarter of a century working at the business his grandfather came to Cambridge to run more than 80 years ago.
You might expect a family firm of such standing to be stuck in the past, but Turvill explains that Swiss Laundry has not only survived but thrived - and created new jobs - by actively embracing change and seeking out more productive ways of working.
One of the biggest challenges to face the business, which has two factories in East Anglia, was the 1999 introduction of the minimum wage. Staffing costs rocketed, and to meet this new financial load, firms in all sectors had to find more efficient ways of working, which meant investing in new technology.
Subscribe to The Week
Escape your echo chamber. Get the facts behind the news, plus analysis from multiple perspectives.
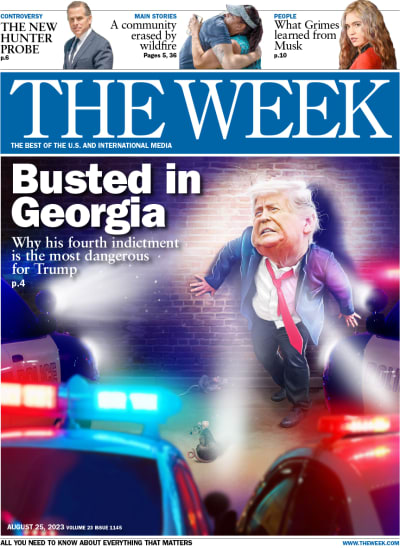
Sign up for The Week's Free Newsletters
From our morning news briefing to a weekly Good News Newsletter, get the best of The Week delivered directly to your inbox.
From our morning news briefing to a weekly Good News Newsletter, get the best of The Week delivered directly to your inbox.
“There was a drive for investment - and that hastened consolidation because a lot of businesses were under-invested,” recalls Turvill. In 2004, Swiss Laundry itself played an active part in the consolidation, buying Camplings Linen in Great Yarmouth.
“You have to make a decision whether to play the game or close the door,” says Turvill.
A new type of automation
It was another crunch investment decision that brought the Turvill family and Lombard together. In 2016, when Swiss Laundry decided to invest heavily in automation, Lombard helped finance a new type of production line at the company’s Great Yarmouth plant.
A free daily email with the biggest news stories of the day – and the best features from TheWeek.com
Turvill explains: “Historically, staff would open a hamper of dirty linen and sort it on a table. More recently, the linen comes in bags and cages and is emptied onto a conveyor. It goes past people who pull out items and throw them into apertures for each category of linen.”
In that way, pillowcases, duvet covers and sheets can be separated for processing. But with Lombard’s support, Swiss Laundry has been able to go several steps further, embracing the possibilities for increased productivity offered by computer automation.
“What Lombard has helped us finance,” says Turvill, “is an overhead bag system that allows us to sub-sort linen into 50kg bags which are stored in the air on a monorail network. And this is computerised, so we know what’s in the air in terms of sheets, duvet covers and pillowcases, and we can wash them to order.”
Bridging the productivity gap
- Podcast
The productivity conundrum: how technology could fend off the risk of recession
Listen to podcast
- Insight Report
Automation and the productivity challenge
Download now
- Age of Disruption
Embracing business agility in an ever-changing world
Learn more
The new, fully-automated line came into service in 2017, and its value to the company is demonstrated by the decision to replicate the system at Swiss Laundry’s new factory at Papworth, near Cambridge.
Once again, Lombard is financing the plant. They are providing £2.5m towards the project, out of a total spend of £6m on equipment at the brand-new facility, which replaces the firm’s older Cambridge factory.
Turvill recounts: “We approached Lombard and they shared our vision in what we were trying to do and provided us with flexible credit lines. We formed a great working relationship with Mark Coe and Rachel Humberstone at Lombard.”
Bad news for low-skilled staff?
One of the fears often voiced about automation is that it takes away jobs, especially for low-skilled workers. This can be seen as a problem - or, more constructively, as an incentive for firms to train staff and for the UK to improve standards of education.
So what impact did transforming the way laundry is sorted have on staffing at Swiss Laundry? “What we’ve found is that, with the growth of our business as a result of automation and investment, we’ve actually increased our staffing,” says Turvill. “Some roles have been changed but with greater capacity, there’s also been job creation. The laundry is operating for longer hours and processing many more pieces, enabling us to extend our customer portfolio and meet the laundry needs of more hotels, restaurants and tourism businesses throughout East Anglia.”
It seems counter-intuitive, but by adopting technology that allows Swiss Laundry to reduce labour, the firm has actually created new jobs. And each worker is now 30% more productive, as well as more comfortable at work: the new machinery massively reduces manual lifting, pulling and twisting of heavy laundry bags.
Being more efficient means the business can offer a more competitive price to customers - and is expanding as a result. What’s more, these new jobs are more highly skilled and therefore more secure.
“Providing people with job security is very important to us as a family business,” says Turvill. “We have people who are incredibly loyal, working for us for decades.” With a total staff of 250, plus some seasonal roles, Swiss Laundry has a direct connection to its employees in the way some larger firms do not.
Automation has other benefits, says Turvill: “The use of conveyors and ergonomic delivery of linen throughout the factory reduces manual handling, improves efficiencies, and, overall, creates a better place to work.”
To find out how Lombard could help your business or to get a free quote, visit Lombard.co.uk, call us on 0800 502 402, or text Relay 18001 0800 502 402
Security may be required. Product fees may apply. Finance is only available for business purposes