Cluny lace: keeping traditional manufacturing alive
Ninth-generation lace-factory owner Charles Mason discusses the dying art of traditional lace-making
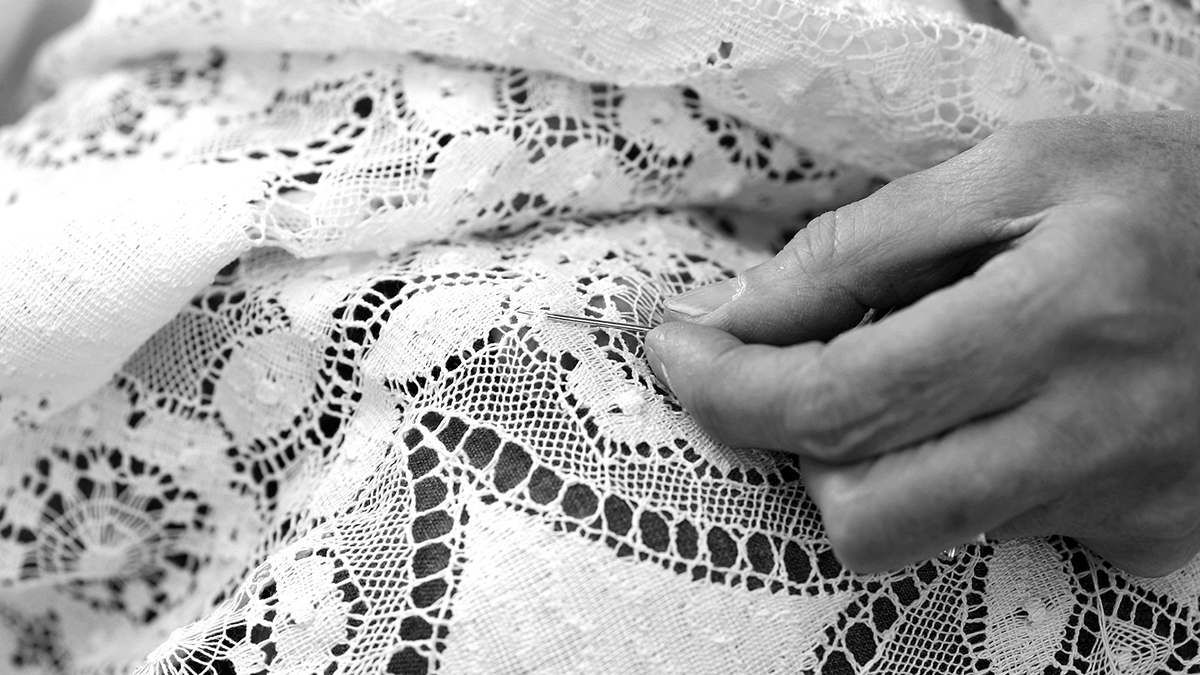
I’m the ninth generation of my family to be in the lace trade. The Cluny Lace factory, near Nottingham, was built in the 1880s, but we had machines in Ilkeston and Long Eaton before then. By the 1730s, my family were already framework knitters and flax dressers, and they began making lace in the 1760s, at the start of the Industrial Revolution.
The lace we make here imitates some handmade-lace designs, and the construction is as close to handmade lace as a machine can do. Lace was originally made with linen or silk threads, but now it’s often made using cotton.
We use a traditional Leavers lace machine, which is actually two combined in one: a wide machine, working on the principle invented by John Leavers in 1813, which twists the threads to form a net, and a jacquard machine that adds pattern, turning a basic net into exquisite lace. I started working here in 1987, at a boom time for Raschel lace, which is used for most lingerie, bridal and fashion lace these days. Raschel lace is lower-quality than Leavers lace, but quicker to make.
The Week
Escape your echo chamber. Get the facts behind the news, plus analysis from multiple perspectives.
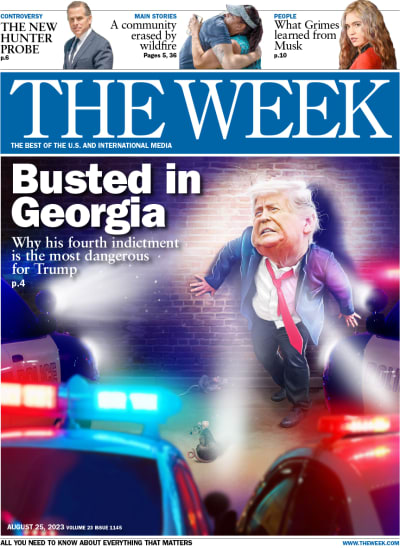
Sign up for The Week's Free Newsletters
From our morning news briefing to a weekly Good News Newsletter, get the best of The Week delivered directly to your inbox.
From our morning news briefing to a weekly Good News Newsletter, get the best of The Week delivered directly to your inbox.
Thankfully, because we are doing well with the Raschel lace, we can afford to recondition the Leavers lace machines. Some were built more than 100 years ago, so it’s expensive to maintain them, but once they’ve been reconditioned, they will last for up to 40 years. I’m still learning about the machines even now, as they involve so many different aspects of engineering. There are no instruction books, either, so it’s definitely a case of learning from experience.
We have a pattern archive that runs into thousands – each one is numbered and no other manufacturer in the world can produce the same design. The patterns come from a mixture of sources and many have been designed by people who’ve worked at the Cluny factory in the past, such as my grandfather Francis Bowler Mason and his father, Frank Maltby Mason, who were designers and draughtsmen. Many were inspired by old, handmade patterns, and while it’s difficult for us to make a brand-new design, we can adapt old ones.
Most lace is made in the Far East now – large quantities of British lace used to be exported to Hong Kong, but many of the British underwear factories began sourcing in Hong Kong and then started garment-making there, too.
This was really the catalyst for the demise of British lace and, eventually, most European lace, as the Chinese were able to buy machines from Germany and make the lace themselves at a much better price.
A free daily email with the biggest news stories of the day – and the best features from TheWeek.com
There are still some lace factories left in France, a couple in northern Italy and one in the States, but they tend to make slightly different styles of lace to ours, and use mainly synthetic fibres, such as nylon.
It’s hard to say what the future holds for this factory – almost half of our team of 22 workers are around retirement age, and that’s a problem. I do wonder what will happen to the next generation, and who will be able to recondition the lace machines. There are people here in the UK who can take care of the basics, but even they will be retiring in the next 20 years, so who’s going to follow them, I don’t know.
Charles Mason owns the Cluny Lace factory in Ilkeston, the last remaining British manufacturer of traditional Leavers lace. He studied textiles at the University of Leeds before taking on the family business; clunylace.com
-
August 31 editorial cartoons
Cartoons Sunday’s political cartoons include FEMA's new scheme, Gavin Newsom's antics, and a clue in the Epstein files
-
Disarming Hezbollah: Lebanon's risky mission
Talking Point Iran-backed militia has brought 'nothing but war, division and misery', but rooting them out for good is a daunting and dangerous task
-
Woof! Britain's love affair with dogs
The Explainer The UK's canine population is booming. What does that mean for man's best friend?
-
Cubitts: an eye for the unique
In Depth Founder Tom Broughton on harnessing traditional hand-craftsmanship and modern technologies for a new chapter in London spectacle making
-
The daughter also rises: remembering the work of May Morris
In Depth A new exhibition at the William Morris Gallery focuses on his youngest child, one of the forgotten heroines of the Arts and Crafts movement
-
Petersham Nurseries comes to Covent Garden
In Depth Managing director Lara Boglione on bringing a taste of the popular Richmond garden shop and cafe to central London
-
Grain & Knot: A cut above
In Depth Founder Sophie Sellu on leaving her office job to start her own business hand-carving wooden utensils
-
The New Craftsmen: Discover beautiful British crafts
In Depth Co-founder Natalie Melton talks about the challenges facing makers today and the joy of handmade homeware
-
London Craft Week: Discover makers, designers and artists
In Depth Over 100 of the UK's top talents are opening their studios for tours and masterclasses for a behind-the-scenes glimpse at their work
-
Cheaney & Sons: The changing business of brogues
In Depth William Church of the Northampton-based shoemakers talks about the future of British-made brogues
-
School of rock: Create objets d'art with a master craftsman
In Depth Want to fashion your very own masterpiece? Ditch night school and enrol with an established atelier