Peter Bellerby: Bespoke Globes
The founder of Bellerby & Co describes the patience, skill and determination it took to revive the lost art of handcrafted globemaking
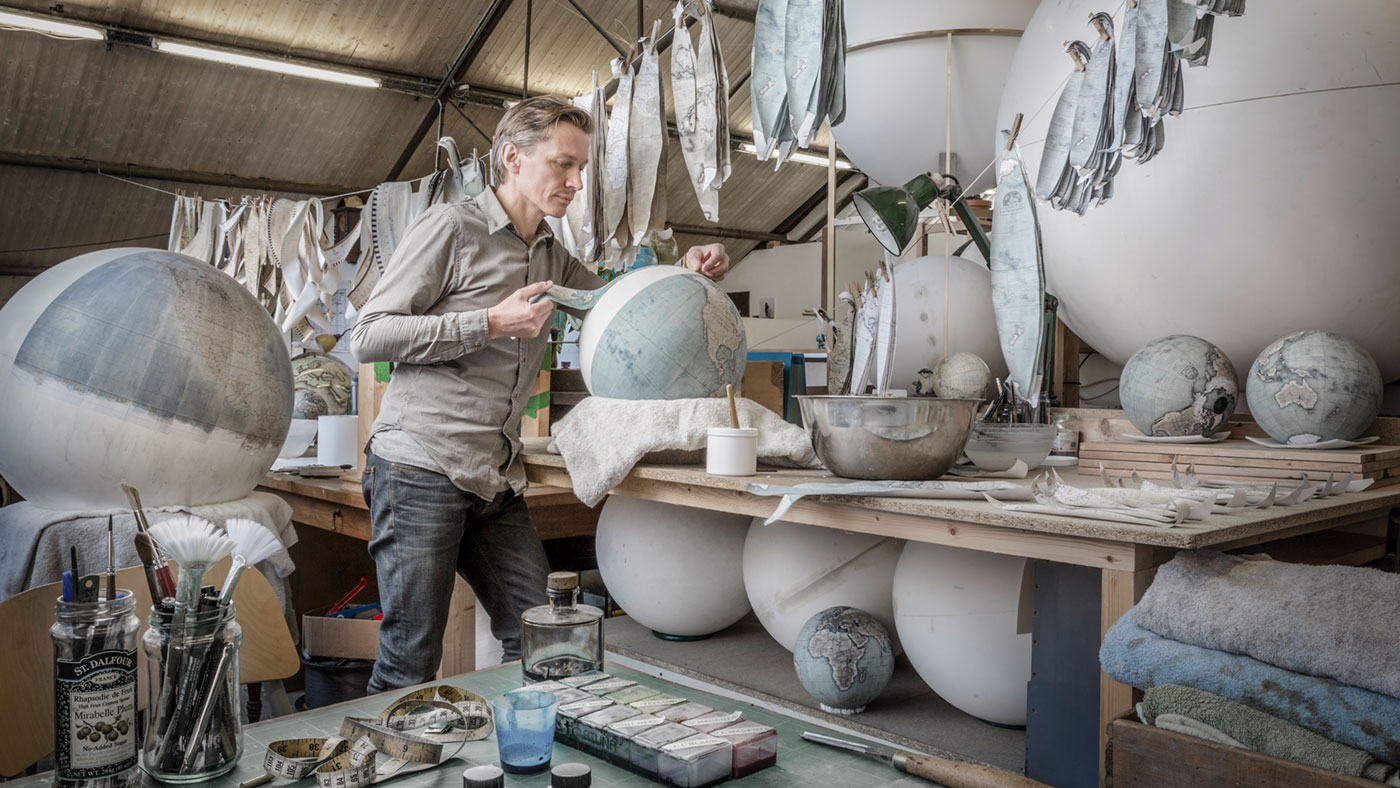
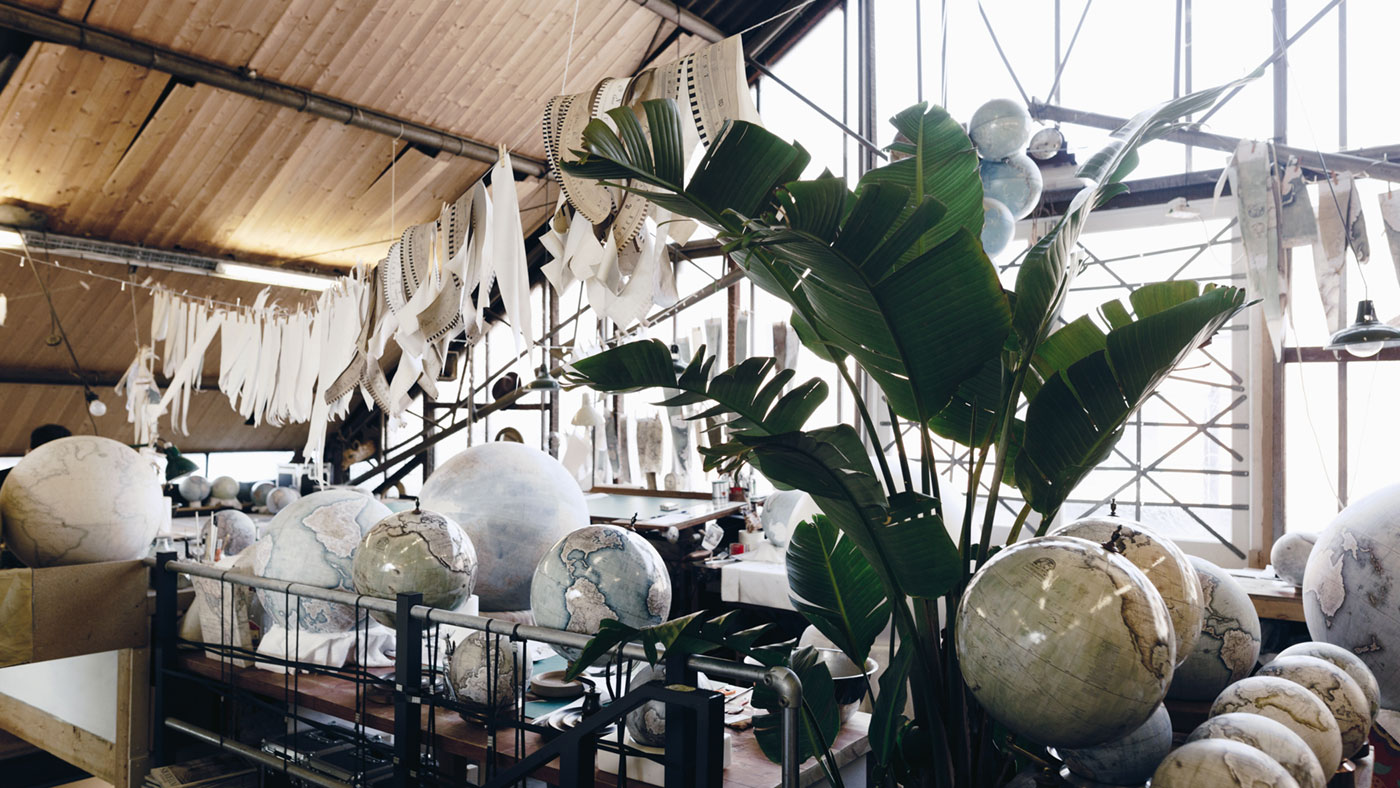
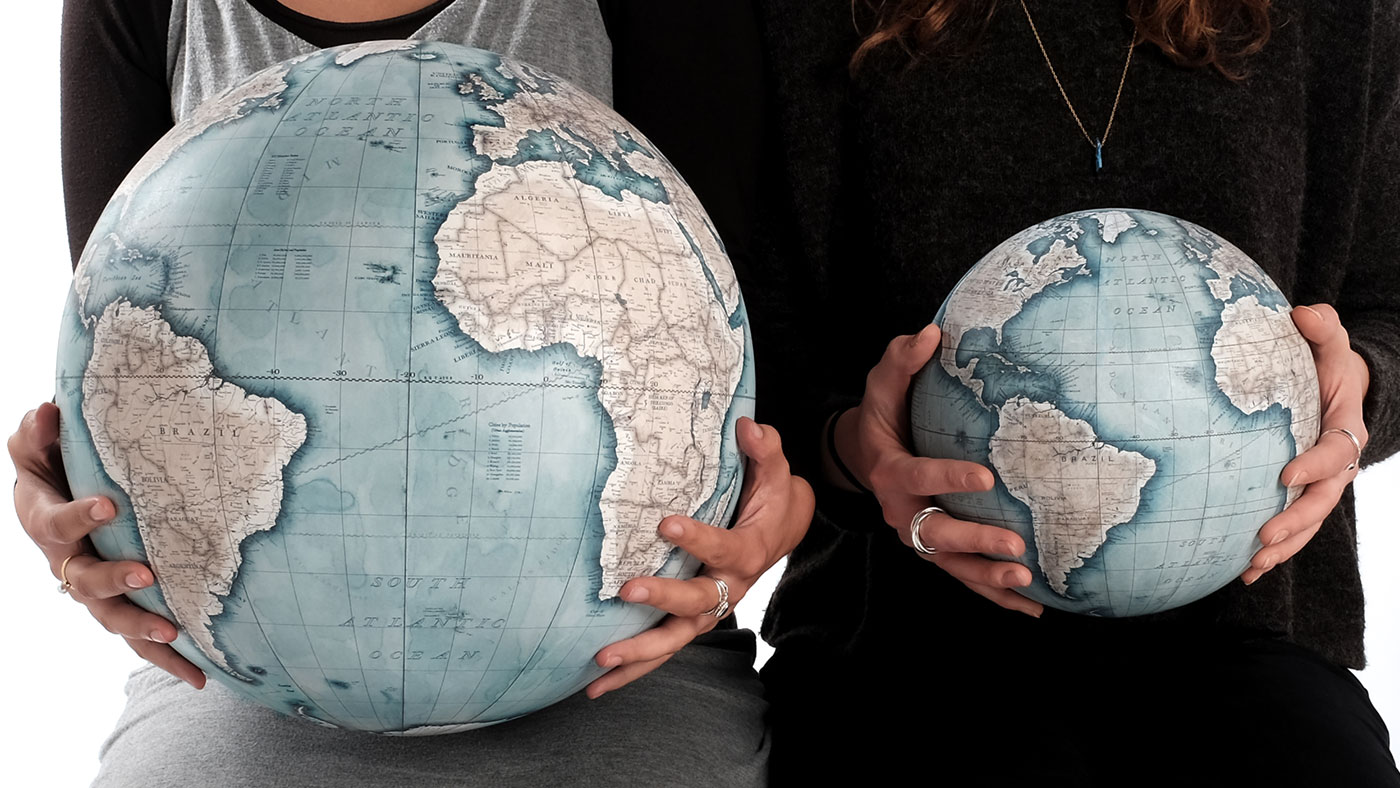
I started making globes as a hobby. I wanted to purchase one for my father’s 80th birthday, but after searching quite extensively could only find poor quality reproductions, factory-made plastic versions or fragile and very expensive antiques. I thought, 'How hard can it be?' and set off on a mission to create one. Once the budget had been blown a few times over, and I still had not figured out how to properly make a globe, stubbornness set in. The project ended up taking me two years.
I was surprised to find there were no how-to manuals, from start to finish everything was a challenge. But I got great joy from learning by trial and error, and the eureka moments as things started to make sense. It also means that the way my company makes globes is entirely unique to us, which I think is quite fun.
Firstly, you need to create a perfect sphere, using two half-moulds. My first globes were made using plaster of Paris, but for the larger globes we now use modern composites and the smaller ones are made from resin.
Subscribe to The Week
Escape your echo chamber. Get the facts behind the news, plus analysis from multiple perspectives.
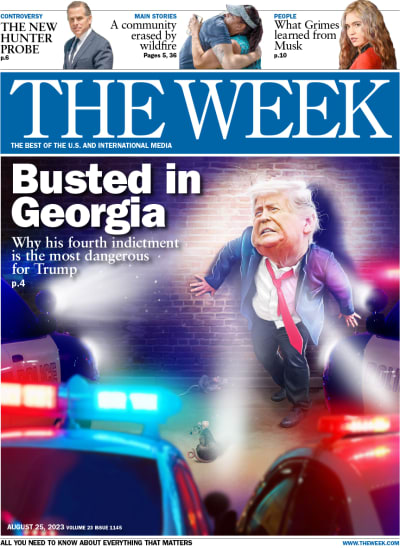
Sign up for The Week's Free Newsletters
From our morning news briefing to a weekly Good News Newsletter, get the best of The Week delivered directly to your inbox.
From our morning news briefing to a weekly Good News Newsletter, get the best of The Week delivered directly to your inbox.
Next, we edit our map. Since each globe is made to order we are updating our cartography regularly and will personalise them to suit each customer's preferences. Once the map is ready, it is printed and cut up by hand into precise oval shapes called gores. The gores are painted by hand using watercolours, which gives a unique result for each globe.
Once the gores are dry they are ready to be attached to the globe, which is called 'goring the globe'. This stage requires extremely precise work and is very difficult because you have to wet and stretch the paper, which makes it very fragile.
After the gores are applied many more layers and detail of watercolour are added and the globe is sealed with either a gloss or matte finish and placed into its base. We make a variety of traditional and modern bases of our own design. Everything is bespoke and the customer can choose from a large range of colours, woods and finishes.
There are not many globemakers in the world; we are the only company handcrafting and hand painting globes. The commercial makers all print their maps in full colour, and machines apply their gores, but I don't believe you can achieve accuracy doing it that way.
A free daily email with the biggest news stories of the day – and the best features from TheWeek.com
It takes from a few weeks to a few months to make each globe, depending on the size and level of personalisation. When I train a new globemaker – and give them all the tools they need – it still takes them at least six months of daily attempts before they get it right. Beyond anything else, patience is a quality we look for when hiring new members of our team. Most of the day we work in total silence, concentrating on each movement of our hands. It is extremely precise and delicate work.
We are a team of about 20 now. We have two full-time cartographers, woodworkers, painters, globemakers, two new apprentices in training, an illustrator, an engraver, my partner who handles all the marketing and sales side of things, and let’s not forget the accountant.
Our workshop is in Stoke Newington, in a former warehouse down a little mews. It is nice and airy with big windows, high ceilings and full of plants and globes and all the bits and pieces we use to make them. Downstairs we have our woodworking studio where we make and finish the bases as well as the huge space needed to make the 127cm Churchill globes. Upstairs painters, makers and apprentices-in-training all work side by side.
Every day the team takes an hour lunch break together to catch up – on the rooftop when the weather is good. Twice a week they all do yoga together in the studio. It feels more like a family as most of the people have stayed with the company since I first hired them, years ago.
Each globe passes through many hands, with at least five different people involved in the process from start to finish, so there is a lot of teamwork required. In these modern times of technology and mass production, people seem to have newfound respect for traditional crafts. They want something with fingerprints on it, something one of a kind. Handmade globes are a fascinating craft as such an incredible amount of work goes into each and every one.
For further information about Bellerby & Co Globemakers, or to discuss a bespoke commission, visit bellerbyandco.com
-
The US Open's controversial 'superstars' doubles format
Talking Point New shortened competition attracts star pairings and bigger audiences to grand slam tennis event
-
Sudoku medium: August 21, 2025
The Week's daily medium sudoku puzzle
-
Sudoku hard: August 21, 2025
The Week's daily hard sudoku puzzle