Boxing clever: the new generation of prefab homes
Innovative, environmentally friendly and reasonably priced prefabricated homes could be the solution to the housing crisis
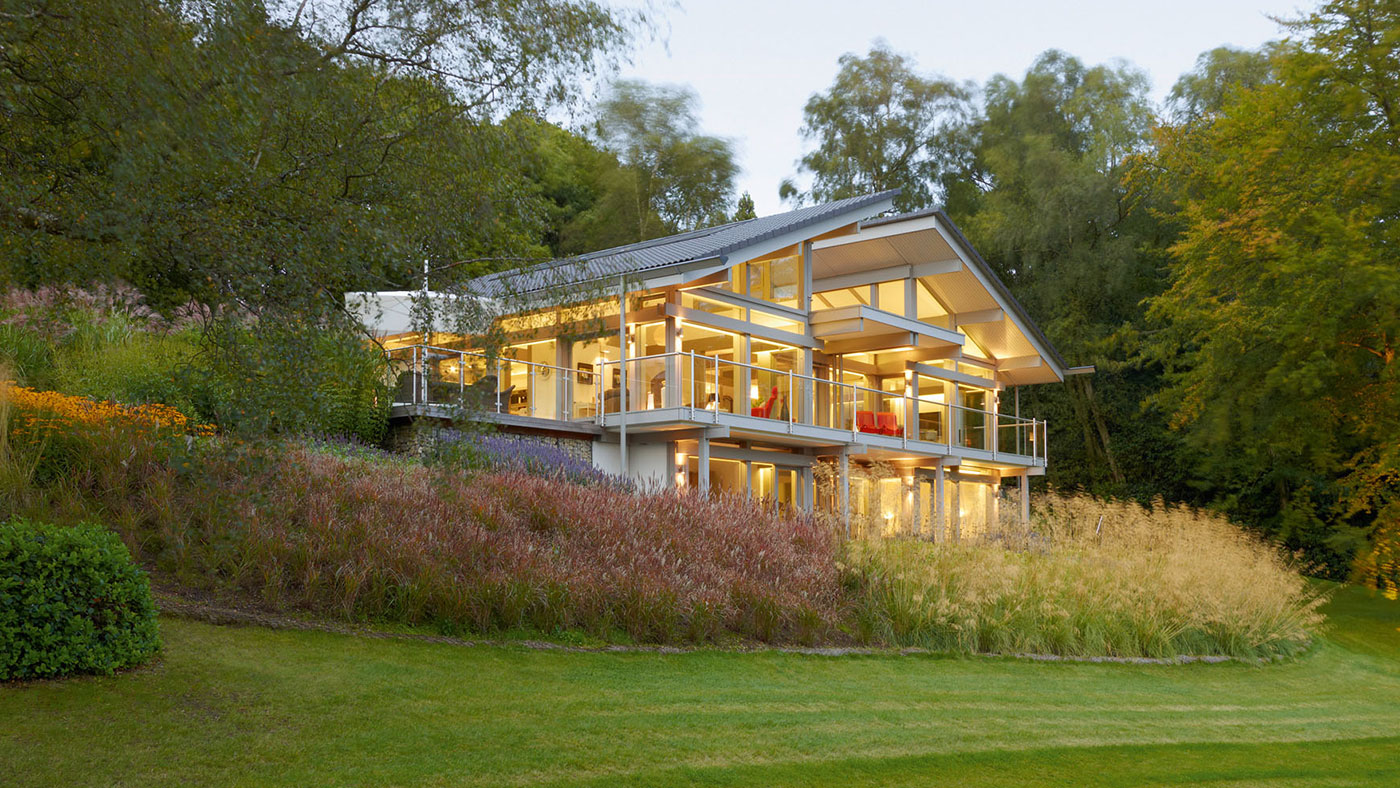
In the late 1960s, Richard Rogers designed a home for his parents at 22 Parkside, Wimbledon. The simple shoebox design used a new kind of prefabrication system, where the individual modules were constructed in a factory then sent to Wimbledon, where the whole thing was put together in a matter of days like giant flat-pack furniture. Rogers' ultimate ambition was that this type of build could eventually be one "bought in a shop". In an interview with online design hub Dezeen, he revealed his initial hopes that the standardised system "would solve the whole of the British housing crisis". It didn't, he conceded, but the project would go on to inspire many of his most iconic designs. The Grade-II listed Wimbledon building was eventually donated to Harvard University and now houses graduate students in an ongoing residency programme, effectively nurturing the next generation of architects.
In reality, prefabricated houses are nothing new. The biggest drive for them was in the late 1940s, when more than 156,000 were built in the UK following the Second World War. Back then, 'prefab' was a byword for poor quality, but advances in technology have vastly improved the output. And while cutting costs and halving construction time are still the primary benefits of prefab, modern renditions are equally concerned with quality design, sustainability and longevity.
Undoubtedly the luxury prefab posterboy is Huf Haus, a third-generation German company founded in 1912. Huf Haus builds are characterised by their visually striking glass and timber frames. Each one is pre-built in a factory in Hartenfels, west Germany before being transported by lorry to its final destination, where it's then constructed on-site by identikit German builders with trademark speed and efficiency. The Germans and Scandinavians may be prefab pioneers but clearly Britain has an appetite for it too, being home to the second-largest Huf Haus market behind the host nation.
Subscribe to The Week
Escape your echo chamber. Get the facts behind the news, plus analysis from multiple perspectives.
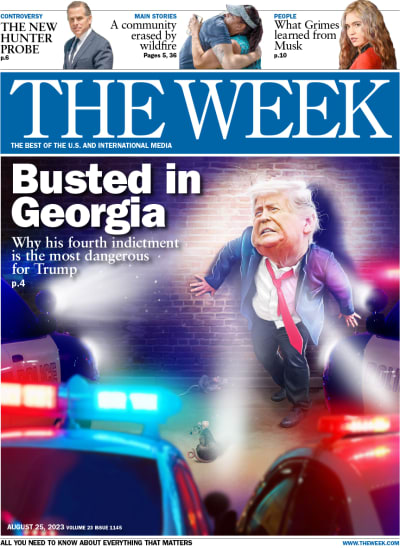
Sign up for The Week's Free Newsletters
From our morning news briefing to a weekly Good News Newsletter, get the best of The Week delivered directly to your inbox.
From our morning news briefing to a weekly Good News Newsletter, get the best of The Week delivered directly to your inbox.
Not only do Huf houses look the part – and when it comes to size and finishes, the sky's the limit – but they're also incredibly energy-efficient, utilising sun, air, soil and even a pioneering ice storage tank system to heat and cool the house. The typical cost works out at around £200 per square foot, including on-site assembly and interior finishes but not, crucially, the plot of land. In 2016, an eye-catching 6,000sq ft Huf Haus in Surrey known as The Lake House, complete with its own helipad, went on the market for a record-breaking £5m.
Image courtesy of Ryohin Keikaku Co., Ltd.
But when it comes to modular homes, it's not always a case of the bigger the better. Running parallel with the current 'slow living' and 'keep it simple' trends is a drive for small builds over grand designs. Dubbed the 'tiny house movement', these small-scale houses echo the simple shoebox designs of the 1950s but with much more architectural distinction. Last year, Japanese minimalist brand Muji began selling their compact 'hut concept' at just £21,000 (so far only available in Japan) which it describes as being 'somewhere between a permanent residence and a holiday home.' At 9sq m it may be smaller than your average London bedsit but it's a real thing of beauty, designed to blend in with nature in trendy Japanese burned cedar and mortar flooring with a large front window and porch.
Also championing the simple approach, but with a more philanthropic ambition, is award-winning Modulhus – aka Snug homes. The Bristol-based company was founded in 2013 to help people "custom-build their own affordable, adaptable and environmentally friendly homes and communities". Unlike Rogers' standalone home, the 'Snug' project is community-centric and the company is continuously involved in outreach work as part of a wider discussion on affordable housing. The simple, customisable modules are designed to be slotted together to create terraced houses or even stacked to make flats. Modulhus created a buzz after winning first prize at the international Self Build on a Shoestring competition and is being hailed as a carbon footprint-friendly solution to Britain's housing crisis and a way for people to realistically afford their own home. A standard 66sq m two-bedroom home is billed at just under £50,000, excluding land.
A free daily email with the biggest news stories of the day – and the best features from TheWeek.com
As populations continue to swell worldwide, residential construction on a large-scale is surely the way forward. And as technology continues to rapidly change the way we work and live, it was only a matter of time before the two integrated.
Katerra is a Silicon Valley-based tech company intent on revolutionising the construction industry. A one-stop design and build shop, Katerra operates all aspects of the process – from schematic design to fabrication of parts and on-site construction – in order to "remove unnecessary time and costs from the building process while also providing world-class design".
Katerra is the brainchild of architect Craig Curtis and tech figurehead Michael Marks, former CEO and chairman of Flextronics International Ltd. In just three years, the company has gone from a start-up to having more than $1.3billion in bookings following a whopping $865m cash injection from SoftBank. Projects are grand in scale and ambition but their roots still lie in the humble prefab template, with various building components and materials pre-built in Katerra's "Integrated Factory" in Phoenix, Arizona. So far, the company portfolio includes the 360-unit Snohomish Garden residences in Seattle, and Union South Bay in California – a swish residential complex designed in collaboration with Architects Orange, complete with a pool, rooftop courtyard, spa and separate retail destination.
"It always takes a company from outside to come into the industry, to recognise that things could be done differently and do them differently," explains Marks on Katerra's vision. "We're taking the technology tools and experiences we have from other industries and applying them to an industry that needs it – there's a lot of room for change."
-
5 museum-grade cartoons about Trump's Smithsonian purge
Cartoons Artists take on institutional rebranding, exhibit interpretation, and more
-
Settling the West Bank: a death knell for a Palestine state?
In the Spotlight The reality on the ground is that the annexation of the West Bank is all but a done deal
-
Sudoku medium: August 23, 2025
The Week's daily medium sudoku puzzle