Inside Chanel's very special handbag atelier
Where runway accessories and signature quilted handbags are crafted with passion and precision
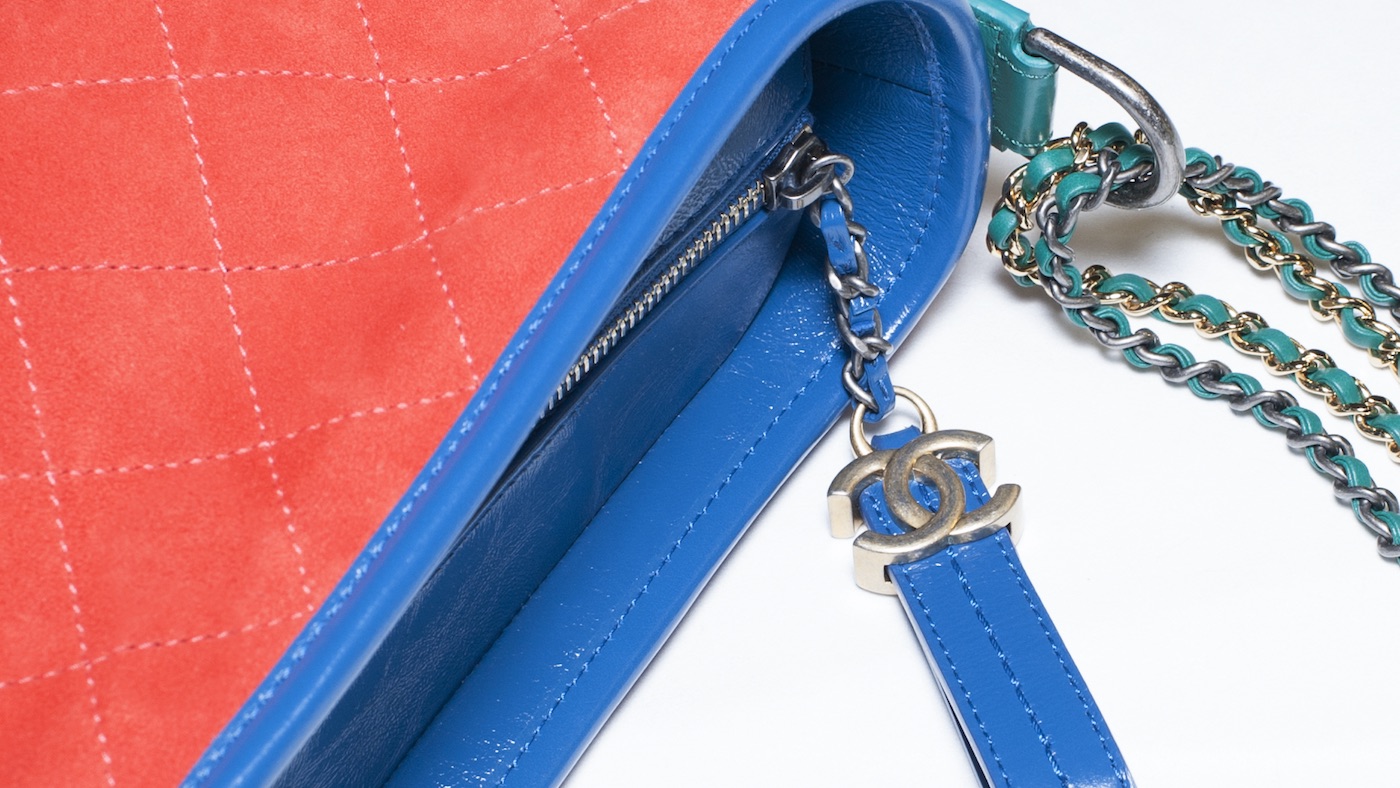
An hour’s drive north of Paris sits Les Ateliers de Verneuil-en-Halatte, an unprepossessing building that looks as if it’s been dropped from the sky like a giant Tetris block. But the site’s prescriptively industrial exterior belies the magic that happens within: it is here that the Chanel’s incredible collection bags are made in specialised workshops.
Every season, catwalk pieces and prototypes are stored away in its sprawling archives. The brand’s classic chain-handled bags – the Boy, the quilted 2.55 and 11.12 handbags, as well as the all-new Gabrielle – are here in every flavour imaginable: adorned with silk flowers, pompoms or charms; decorated with mirrored gems and beads; festooned with silver studs and/or pearls; trimmed with shearling, feathers, criss-cross ribbons or embroidered lace. There are hybrids of leather and denim, flamingo pink suede, Persian blue tweed and ruby velvet; bags crafted from delicate hides that have been treated or manipulated, some laser cut or bearing digitally printed patterns, others with the famous logo in a delicate woollen dust.
Among the more playful highlights is a special SS17 edition of the Boy, covered in crystal stars that glow thanks to LED technology. But the archive is also home to new handbag styles, from jumbo totes and micro bags – worn on ankles for SS08 – to showstoppers such as the maison’s famous SS13 giant ‘hula hoop’ bag. This fun oversize creation comprising two connected hoops cradling a white quilted bag in the shape of a half moon is the most complicated piece the workshop has ever manufactured, according to the Ateliers Verneuil’s general director, Rodolphe Maucolin.
Subscribe to The Week
Escape your echo chamber. Get the facts behind the news, plus analysis from multiple perspectives.
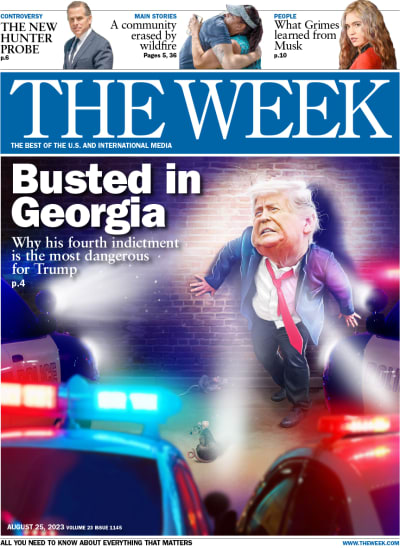
Sign up for The Week's Free Newsletters
From our morning news briefing to a weekly Good News Newsletter, get the best of The Week delivered directly to your inbox.
From our morning news briefing to a weekly Good News Newsletter, get the best of The Week delivered directly to your inbox.
The ateliers are responsible not only for the creative development of all Chanel runway bags and leather accessories, but also their production on an industrial scale for the maison’s global network of boutiques. This is also where non-seasonal bags including the iconic black 2.55 are made, as well as more rarefied accessories such as quilted leather golf bags, and handlebars for deluxe Chanel bicycles.
Remarkably, all runway pieces are created in just three to four weeks, and are sometimes delivered to the show only 24 hours before their big reveal; this process happens six times a year for the two ready-to-wear and two couture collections as well as Cruise and pre-Fall.
Once a core team of 30 design 'developers' receive Karl Lagerfeld’s sketches from his Chanel studio in Paris, they must act fast to decipher the exact dimensions of each bag and enlist the aid of in-house model-makers to construct prototypes from a bonded leather called salpa, which are then sent back to Paris for comment. Next, the team must determine components such as zips, chains, charms and clasps in relation to the proposed material, be it fabric, leather, denim or PVC. This small group must also work with tanneries to find solutions to often complex ideas, with the aim of honouring Mr Lagerfeld’s drawings. "It’s impossible for us to say no to the studio," says Maucolin, who is the eyes and ears of the ateliers.
Maucolin oversees all aspects of production, which starts life on the catwalk and moves into what he calls "artisanat industriel": manufacturing by a highly skilled workforce whose craftsmanship is done by hand but aided by sophisticated machinery. "Chanel is a fashion brand; it is our DNA," he says. "More than 80 per cent of our production is new bags – classic bags we produce, of course, but always at the same time as the seasonal collections."
A free daily email with the biggest news stories of the day – and the best features from TheWeek.com
The Ateliers Verneuil are part of Chanel’s ‘Paraffection’ ('for love') scheme, an initiative that aims to promote and preserve the savoir faire of artisan houses through its acquisition of Métiers D’Art firms producing couture goods for Chanel and other prestigious houses. "It’s important to work with other brands, because their ways of working will help to develop our own know-how," says Maucolin. "Today we’re the first leather goods company for haute couture. We’re working with young designers, and we make bags for a number of haute couture labels." (Sadly, confidentiality clauses forbid him from disclosing which.)
Every Chanel bag is assembled by a team of four artisans, with, on average, 200 operations involved; this year’s Gabrielle handbag goes further with approximately 300. Designed by Lagerfeld and named after the maison’s visionary founder – better known as 'Coco' – the Gabrielle is the first bag to join Chanel’s classic line in five years. It’s a truly modern addition, too, not least because its rigid base was inspired by the shape of VR goggles. It’s also the first Chanel bag to combine different coloured chains: silver, gold and sometimes metal- black ruthenium. More playful and versatile than any Chanel classic to date, it can be worn a number of ways, chiming with Coco’s prescient belief that "elegance in a garment is the freedom of movement".
Work at the Ateliers Verneuil rarely slows: August is a quieter month for the workshops, but otherwise this is a firm in constant flux. "In production, you have to be cent pour cent," says Maucolin with a knowing smile.
Once runway bags are approved for large-scale production, all departments must work in tandem to get the collection to the boutiques on time. This means the acquisition, coordination and testing of around 17,000 components per collection. Every piece of leather and fabric is examined; every screw, stud and charm must pass rigorous quality control. “The leather may be perfect [after initial testing] but when everything is put together, this combination of elements may cause problems,” says Maucolin as we enter a lab-like testing room, where a blue calfskin Boy bag is locked in an amber-lit chamber like some exotic zoo specimen. "It’s 65°C and 95 per cent humidity in there. So it’s like putting a bag in the jungle!"
A Chanel bag must, after all, wear just as well in tropical climates as it does swinging on the arm of a city dweller in Europe. Elsewhere in the testing room, workers perform abrasion tests on swatches of new leather; one lady is carrying out a 'sellotape' test on button studs to ensure they lose none of their metallic sheen. "Everything must be perfect," says Maucolin. "The atelier is in perpetual movement. It is like a heart, you know; sometimes it beats very quickly."
In the four sewing/assembly workshops, a sense of calm prevails. One area is dedicated to the making of the rubans en cuir – leather strips inserted by hand into the famous chain straps – and there’s a table where ‘la patte’ (the tab supporting the clasp of the 2.55 and 11.12) is put together. "Just making this part by hand is crazy," explains Maucolin, picking up a box of multicoloured leather tabs. "Gabrielle Chanel created her bags like ready-to-wear. That is to say you work on an area then turn it inside out so you don’t see the sewn parts. We still do this."
There are as many as 50 geometric parts to a Chanel bag, necessitating a lot of concealed stitching. Digitally operated sewing machines combine some leather sections with foam to create the signature quilting, or matelassage, but it is up to the predominantly female workforce of the sewing ateliers to assemble the panels to exacting measurements. "They work to the millimetre – sometimes under the millimetre," says Maucolin.
A case in point is the rectangular metal clasp of the Boy, which must sit exactly on the last stitch line of the handbag’s front flap, with its top corners touching a diamond point of the quilted leather. Pieces that don’t meet this standard are destroyed, although this happens only rarely, says Maucolin: “It takes four to five years to learn how to fully assemble a Chanel bag. It’s the most complicated job here.
Spared such a tragic end are the damaged Chanel bags received from clients for repair. These are restored in 'La Clinique', where ‘surgeons’ replace missing metallic parts as well as leather. The team’s most challenging casualty to date was the result of an ambitious craft project. "The young son of a famous footballer cut out the CC logo of his mother’s Cambon tote," laughs one repairer. "We had to completely replace the front and side panels, and, of course, add a new logo."
Next up is a scuffed and faded cross-body bag, lovingly worn for almost two decades. The connectors that hold the chain in place have all but disintegrated, and much to the repairers’ surprise, the instruction docket notes the client’s desire to simply replace these small parts so that the beloved bag can once again be worn with pride, scuffs and all.
"This is one way to wear history," says my guide, perhaps unaware that he is echoing the sentiment of Gabrielle Chanel herself, who famously stated, "Fashion fades. Only style remains the same."
Images by Lucy Sparks
-
Why Penelope Cruz is an expert in Chanel, both on and off-screen
Under the Radar The award-winning actor explains her enduring relationship with the Parisian fashion house
-
N°1 de Chanel: sustainability in heritage
Under the Radar A new skincare and beauty collection by Chanel researches the camellia
-
Coco vision: up close to Chanel opticals
Speed Read Parisian luxury house adds opticals to digital offering
-
Look twice: Chanel Factory 5 opens at Selfridges London
Under the Radar Factory 5 collection celebrates the fragrance’s centenary
-
Charlotte Casiraghi’s Chanel moments
Under the Radar Casiraghi takes us backstage at Monaco villa La Vigie for her Chanel debut
-
Chanel Connects: Paris brand launches new podcast series
feature Tilda Swinton, Edward Enniful and Nicholas Cullinan feature on the first episode
-
Beautiful science: Chanel’s open-sky labs
Speed Read Botanical wonders lie at the heart of Chanel’s science-led skincare
-
Patrice Leguéreau: Chanel's master of stones
In Depth Patrice Leguéreau is the secret weapon behind Chanel's spectacular jewellery collections