Max Mara: a glimpse inside the iconic brand’s manufacture
Max Mara’s manufacture of dreams where coats are made with laboratory-like precision
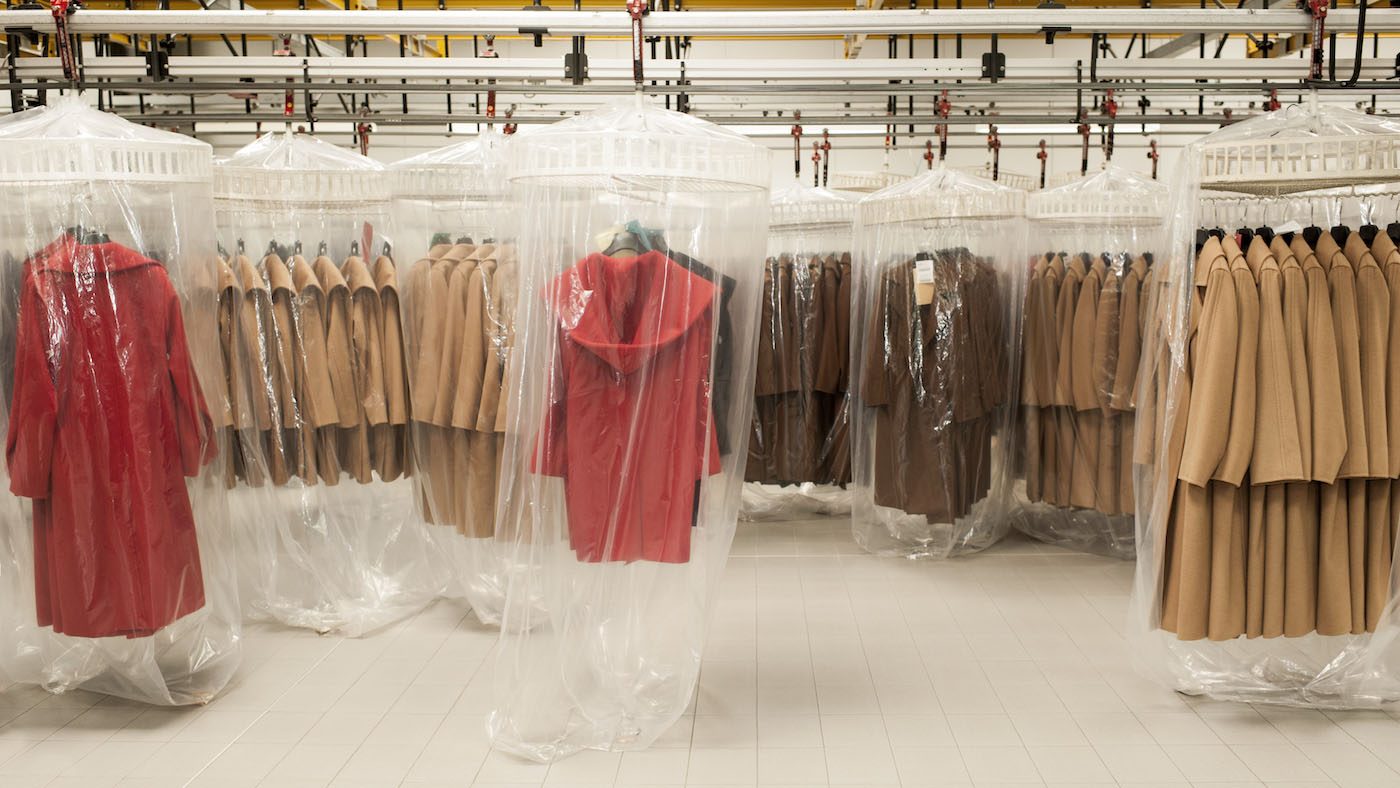
In 2003, the Max Mara Fashion Group moved into its new headquarters, designed by John McAslan + Partners, the London-based firm behind Qatar’s imposing Park Hyatt Hotel and the transformation of King’s Cross railway station. The architects envisioned a campus-like complex that would promote collaboration between the group’s employees and nine brands, which in addition to Max Mara include Sportmax, Marina Rinaldi and MAX&Co. Brick, steel and concrete buildings are connected by tree-lined pathways; bridges cross square ponds; floor-to-ceiling windows flood offices with daylight and frame sweeping views of the flat farmlands of Emilia-Romagna.
This region in Northern Italy by the River Po has been the company’s bucolic backdrop since Achille Maramotti established Max Mara as one of Italy’s first ready-to-wear labels in 1951 in the cathedral town of Reggio Emilia. Max Mara’s history can be researched in the company library, which houses more than 6,000 books — on topics ranging from historical dress to socialites’ wardrobes – 350 current magazine titles, and 2,000 rare magazines dating back to the early 20th century.
This is but a fraction of the firm’s fastidiously catalogued archive: a short drive from HQ, a second site stores 600 original sketches, 300 boxes of fabric swatches, and more than 20,000 finished Max Mara garments, which featured in a traveling exhibition that visited Berlin (2006), Tokyo (2007) and Beijing (2008) before arriving in Moscow in 2011 for the brand’s 60th anniversary. Another research collection comprises 4,500 items of clothing and accessories representing various decades from fashion history.
Subscribe to The Week
Escape your echo chamber. Get the facts behind the news, plus analysis from multiple perspectives.
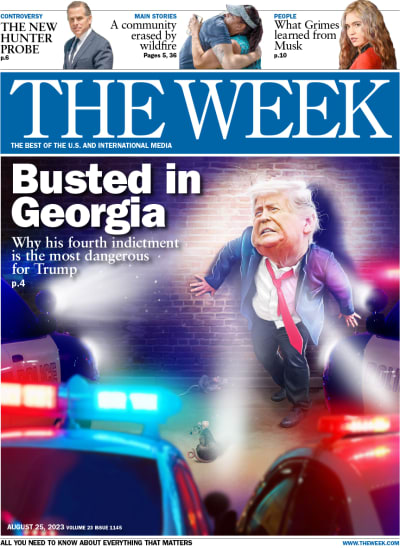
Sign up for The Week's Free Newsletters
From our morning news briefing to a weekly Good News Newsletter, get the best of The Week delivered directly to your inbox.
From our morning news briefing to a weekly Good News Newsletter, get the best of The Week delivered directly to your inbox.
“It’s important to protect and save the history of fashion,” says Max Mara’s global fashion director, Laura Lusuardi, who has been collecting and safeguarding materials from the company’s 66-year existence since joining Max Mara in 1964, aged 18 (her father was one of Maramotti’s first clients). Some of Lusuardi’s most valuable treasures are locked away in glass-fronted wardrobes back at the headquarters; these include a double-breasted Yves Saint Laurent coat worn by Catherine Deneuve in Luis Bunuel’s 1967 film Belle du Jour, and a 1954 white boucle tweed number from the personal wardrobe of Coco Chanel.
It takes confidence for a fashion brand to archive competitors’ work, but Lusuardi’s anthology of famous coats would be incomplete without the 101801. “This is our key coat,” she says of the Max Mara classic. “Like the Kelly bag for Hermes and the trench coat for Burberry.First produced in 1981, the 101801 remains true to the original design sketched by Anne Marie Beretta, the French couturier famed for her sculptural creations. Beretta is one of many high-profile consultants who have worked for Max Mara over the years; Karl Lagerfeld and Jean-Charles de Castelbajac are also on this illustrious list.
A double-breasted creation in 80% wool and 20% cashmere, the 101801 fuses the tailored, draped lines of a man’s overcoat with inset kimono sleeves. Since its inception, the coat has been a worldwide bestseller; it has also been the subject of various artistic interpretations. In 2001, Swiss fashion illustrator François Berthoud superimposed segments of its paper pattern onto camel-toned portraits, and US artist William Wegman’s 2015 exhibition ‘Dogs In Coats’ showed a pack of grey Weimaraners modeling the 101801. Since 2010, the coat has been fitted with an optional belt in matching fabric, pure silk lining, and a label that can be personalised with the wearer’s initials.
Expert in outerwear, Max Mara has since debuted numerous other bestselling designs, including the slim-fitting, wide-lapelled Manuela. The AW17 collection, shown at Milan Fashion Week, experimented with luxurious hybrid designs, adding caramel-coloured shearling collars to camel-hair greatcoats.
A free daily email with the biggest news stories of the day – and the best features from TheWeek.com
Timeless, understated and a feat of ‘Made in Italy’ production, Max Mara’s coats have become emblematic of Achille Maramotti’s pioneering ready-to-wear brand. After graduating in law from the University of Parma, followed by a stint at a Swiss raincoat manufacturer, Maramotti set up his own business in 1951. His family had strong connections to Italy’s dressmaking tradition; great-grandmother Marina Rinaldi supervised a respected tailoring atelier in Reggio Emilia, and his mother Giulia Fontanesi Maramotti taught generations of artisans at her dressmaking school.
Inherited knowledge armed Maramotti with confidence, but it was his pursuit of modernism that really launched his career. In 1957, he returned from a trip to the US inspired by its innovative factories and determined to improve his firm’s productivity without compromising on quality. In addition to meticulously mapped production, Maramotti added direct retail and successfully turned Max Mara into a fashion group with separate lines.
Maramotti retired some time ago, and today the company is steered by his three children. There is a factory in Casalmaggiore, but the other in San Maurizio, where Maramotti moved part of the group’s production in 1988, specialises in coats. The pinnacle of his vision for the garment industry, the purpose-built Manifattura di S. Maurizio produces around 65,000 high-quality garments per year, each requiring 70 to 120 production steps carried out by 230 skilled artisans.
“It’s a very particular laboratory,” explains Giuseppe Bacci, who first started working at San Maurizio in 1977. “I was born here in production, and I will finish in production. Here, one of the main secrets is that style and production work together.”
Set across 10,000 square feet, the Manifattura is designed for end-to-end production, from raw material to finished product. The brand’s craftspeople — a mostly female workforce clad in white lab coats and averaging 35 years in age — produce up to 450 Max Mara coats a day in precisely planned production steps. Currently, there are close to 20 different coat models, each requiring a bespoke process.
While the team is certainly busy, an atmosphere of calm concentration prevails, scored to the rhythmic melody of machines at work and broken only by the sound of an alarm bell signalling espresso breaks. The site’s corridors are adorned with framed Max Mara campaigns shot by Sarah Moon and Richard Avedon, while in the workrooms the art is more convivial: a collage of mementos — personal holiday snaps, postcards, religious iconography — pinned to the walls by the staff. Workers are well looked after at Max Mara: humidity and light levels are controlled, there’s a creche adjacent to the workshops, and an early-start / early-finish rota allows for an even work-life balance.
The plant’s structure was set up close to three decades ago, and its innovative layout has made it a design paradigm. The production of a Max Mara coat begins by building up the ‘mattress’. Up to 20 layers of fabric, each measuring up to 5 m in length, are layered and stretched, before being cut into panels following the coat’s dressmaking pattern, from sleeve to collar. This ensures every Max Mara coat has a uniformity of colour and texture.
The cutting department works from a fact sheet that combines a line drawing with notes and pattern. All material is cut by machine — blades for fabrics, laser for leathers — to precise measurements to minimise fabric waste; the company aims to use 84% of all cloth, and leftover material is collected by a specialist recycling firm. Cutting all the panels for one coat takes around a minute, after which they are measured and placed on trolleys to be transferred to the large sewing room.
Here, tasks are divided into 10 groups and performed by eight to 12 artisans. Each group is overseen by one supervisor controlling quality, production and timing. Extended from the ceiling and moving mechanically between workbenches, a Max Mara coat takes full shape in four to five hours, depending on the model – the 101801 requires 73 stages. Sleeves are inserted and belts added — the team can produce up to 400 belts per day – and numerous quality control and meticulous ironing ‘breaks’ are scheduled between steps. “The ironing is a philosophy,” says Bacci, only half in jest.
Other Max Mara fortes include an array of expert stitching techniques, from the elongated saddle stitch to creating double-face garments and the ‘puntino’ — a signature Max Mara detail. These decorative stitches are crafted using a slow-working machine that mimics the artisan’s hand, using a single long thread and a needle with an open eye. The brand was the first to apply the technique to heavy cloths.
At the Manifattura di S. Maurizio, materials of every coat produced are kept in a special fabric storehouse — from autumnal woollens, alpaca, yak and cashmere cloths to lighter fabrics for the spring. It’s a technique inspired by traditional Italian tailors who would keep a cut of shirting fabric for future repairs, and one that guarantees a Max Mara coat really is for life.
Photography by Lucy Sparks
-
The app tackling porn addiction
Under the Radar Blending behavioural science with cutting-edge technology, Quittr is part of a growing abstinence movement among men focused on self-improvement
-
Magazine solutions - August 29, 2025
Puzzles and Quizzes Issue - August 29, 2025
-
Magazine printables - August 29, 2025
Puzzles and Quizzes Issue - August 29, 2025
-
Friendship: 'bromance' comedy starring Paul Rudd and Tim Robinson
The Week Recommends 'Lampooning and embracing' middle-aged male loneliness, this film is 'enjoyable and funny'
-
The Count of Monte Cristo review: 'indecently spectacular' adaptation
The Week Recommends Dumas's classic 19th-century novel is once again given new life in this 'fast-moving' film
-
Death of England: Closing Time review – 'bold, brash reflection on racism'
The Week Recommends The final part of this trilogy deftly explores rising political tensions across the country
-
Sing Sing review: prison drama bursts with 'charm, energy and optimism'
The Week Recommends Colman Domingo plays a real-life prisoner in a performance likely to be an Oscars shoo-in
-
Kaos review: comic retelling of Greek mythology starring Jeff Goldblum
The Week Recommends The new series captures audiences as it 'never takes itself too seriously'
-
Blink Twice review: a 'stylish and savage' black comedy thriller
The Week Recommends Channing Tatum and Naomi Ackie stun in this film on the hedonistic rich directed by Zoë Kravitz
-
Shifters review: 'beautiful' new romantic comedy offers 'bittersweet tenderness'
The Week Recommends The 'inventive, emotionally astute writing' leaves audiences gripped throughout
-
How to do F1: British Grand Prix 2025
The Week Recommends One of the biggest events of the motorsports calendar is back and better than ever